|
ACCESS THE FULL ARTICLE
No SPIE Account? Create one
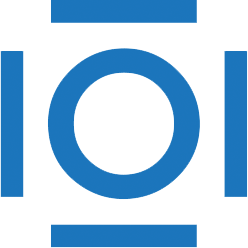
CITATIONS
Cited by 1 scholarly publication.
Crystals
Particles
Metals
Additive manufacturing
Dendrites
Process modeling
Solids