|
ACCESS THE FULL ARTICLE
No SPIE Account? Create one
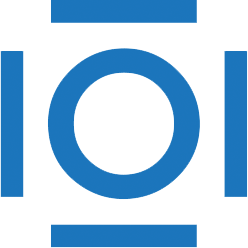
CITATIONS
Cited by 6 scholarly publications.
Resonators
Sensors
Silicon
Electrodes
Glasses
Semiconducting wafers
Electronics