|
ACCESS THE FULL ARTICLE
No SPIE Account? Create one
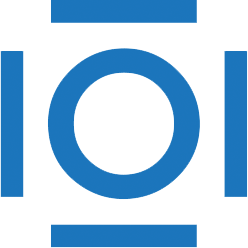
CITATIONS
Cited by 12 scholarly publications.
Manufacturing
Laser welding
Nd:YAG lasers
Aluminum
Optical fibers
Aircraft structures
Carbon dioxide lasers