|
ACCESS THE FULL ARTICLE
No SPIE Account? Create one
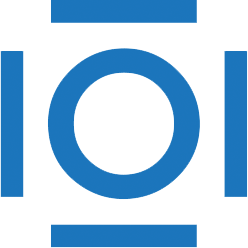
CITATIONS
Cited by 1 scholarly publication.
Actuators
Sensors
Performance modeling
Cesium
Hassium
Optical lithography
Velocity measurements