|
ACCESS THE FULL ARTICLE
No SPIE Account? Create one
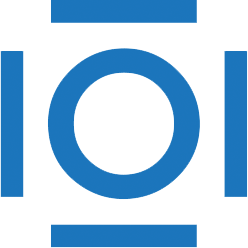
CITATIONS
Cited by 3 scholarly publications.
Actuators
Deep reactive ion etching
Semiconducting wafers
Silicon
Photoresist materials
Microsystems
Materials processing