|
ACCESS THE FULL ARTICLE
No SPIE Account? Create one
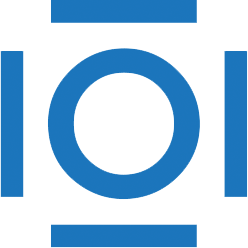
CITATIONS
Cited by 3 scholarly publications.
Epoxies
Adhesives
Temperature metrology
Failure analysis
Aluminum
Data modeling
Finite element methods