|
ACCESS THE FULL ARTICLE
No SPIE Account? Create one
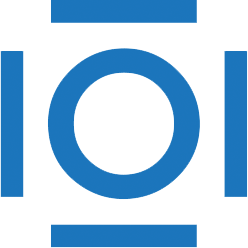
CITATIONS
Cited by 19 scholarly publications and 1 patent.
Electron beam lithography
Semiconducting wafers
Collimators
Electron beams
Wafer-level optics
Lithography
Data corrections