|
ACCESS THE FULL ARTICLE
No SPIE Account? Create one
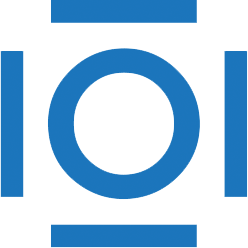
CITATIONS
Cited by 24 scholarly publications.
3D modeling
Microelectromechanical systems
Optical spheres
Data modeling
Scanning electron microscopy
Directed self assembly
Systems modeling