|
ACCESS THE FULL ARTICLE
No SPIE Account? Create one
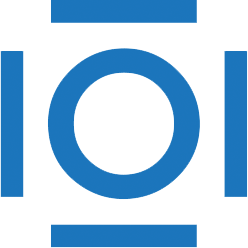
CITATIONS
Cited by 1 scholarly publication.
Data modeling
3D modeling
Numerical analysis
Metrology
Atomic force microscopy
Statistical analysis
3D metrology