|
ACCESS THE FULL ARTICLE
No SPIE Account? Create one
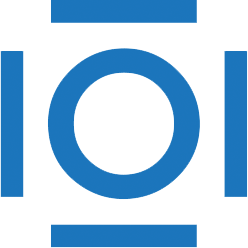
CITATIONS
Cited by 3 scholarly publications.
Semiconducting wafers
Critical dimension metrology
Immersion lithography
Monte Carlo methods
Photomasks
Scanners
Optical proximity correction