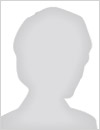
This will count as one of your downloads.
You will have access to both the presentation and article (if available).
The DKIST wavefront correction system will provide active alignment control and jitter compensation for all six of the DKIST science instruments. Five of the instruments will also be fed by a conventional adaptive optics (AO) system, which corrects for high frequency jitter and atmospheric wavefront disturbances. The AO system is built around an extended-source correlating Shack-Hartmann wavefront sensor, a Physik Instrumente fast tip-tilt mirror (FTTM) and a Xinetics 1600-actuator deformable mirror (DM), which are controlled by an FPGA-based real-time system running at 1975 Hz. It is designed to achieve on-axis Strehl of 0.3 at 500 nm in median seeing (r0 = 7 cm) and Strehl of 0.6 at 630 nm in excellent seeing (r0 = 20 cm).
The DKIST wavefront correction team has completed the design phase and is well into the fabrication phase. The FTTM and DM have both been delivered to the DKIST laboratory in Boulder, CO. The real-time controller has been completed and is able to read out the camera and deliver commands to the DM with a total latency of approximately 750 μs. All optics and optomechanics, including many high-precision custom optics, mounts, and stages, are completed or nearing the end of the fabrication process and will soon undergo rigorous acceptance testing.
Before installing the wavefront correction system at the telescope, it will be assembled as a testbed in the laboratory. In the lab, performance tests beginning with component-level testing and continuing to full system testing will ensure that the wavefront correction system meets all performance requirements. Further work in the lab will focus on fine-tuning our alignment and calibration procedures so that installation and alignment on the summit will proceed as efficiently as possible.
View contact details
No SPIE Account? Create one